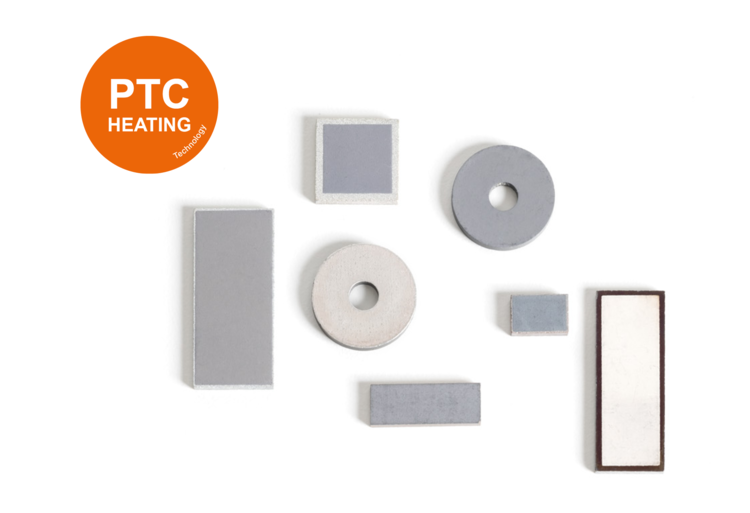
What is PTC?
A PTC, or a semiconductor, is a ceramic-based electrical component with temperature-dependent resistance that is used as a heating element. Its positive temperature coefficient allows electrical current to flow better at low temperatures than at high temperatures. As the temperature rises, the PTC’s natural resistance increases while its current conductivity and power output decrease until a state of equilibrium is reached and the current can barely flow anymore. That’s the so-called PTC effect.
Thanks to their self-regulating characteristic, these kind of heating elements would not be overheat, which makes them particularly safe and reliable.
We make it possible: With PTC
Safe Heating
PTC heating elements come with a fixed maximum temperature which cannot be exceeded due to the PTC effect. Safe heating in protection class II without any additional thermal protection.
Efficient Heating
PTC heating elements dynamically adapt their performance to their environment. Low power consumption at low heat dissipation. Energy-efficient heating without additional temperature control.
Worldwide Heating
PTC heating elements can be operated in a wide range of voltages at almost constant power and are approved to worldwide industry standards. Worldwide heating without additional effort.
Characteristic PTC Curve
The typical resistance curve of a semiconductor as a function of temperature is called PTC curve. The initial resistance of the PTC first decreases slightly with increasing temperature until the lowest resistance value Rmin is reached.
Now its actual behavior begins as the resistance increases non-linearly up to the nominal temperature Tc. At this point, also known as Curie temperature, the PTC’s resistance increases significantly. The operating range of the PTC extends from the nominal temperature Tc to the maximum final temperature Te, where hardly any current flows. The maximum temperature of a PTC depends on its ceramic composition and can therefore be determined in advance.
Another characteristic of the PTC is its inrush current. As the resistance of the PTC is at its lowest value in Rmin, a particularly large amount of current can flow there, causing it to undergo an increased inrush current for a few seconds each time it is switched on.
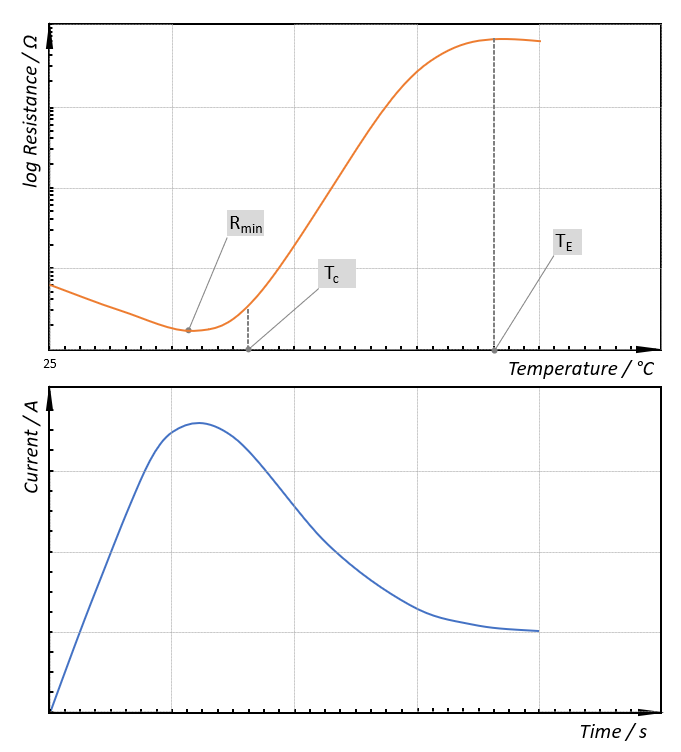
- Multi-voltage capability
Due to the PTC effect and the resulting variable resistance, semiconductors are multi-voltage capable in a defined range. For example, most heaters can operate at 230 V as well as at 400 V without any significant change in power.
- Dynamic power adaptation
The power output of a PTC heating element depends on the heat extraction. If a lot of heat is extracted from the semiconductor, it automatically readjusts its temperature and increases its power. As soon as it reaches its maximum temperature, the power decreases again and hardly any current flows. This dynamic power adjustment makes the heating elements especially energy-efficient.
- Inrush current
PTC heaters experience an increased inrush current for a few seconds each time they switch on. We therefore recommend to use a time-delay fuse in order to protect the application.
- Self-limiting effect
Due to the logarithmic increase of the PTC’s natural resistance in relation to the temperature, the PTC limits itself. As soon as the maximum temperature is reached, the semiconductor becomes non-conductive and settles due to the physical effect. Thanks to this effect, PTCs are particularly safe and do not require any additional thermal fuse.
- Current load for low voltage applications
For low voltage applications, the currents are much higher than for household applications (230 V) due to Ohm’s law. Therefore, it is important to ensure a sufficiently large wire cross-section.
- Power strongly dependent on PTC temperature
The power of a heater is dependent on two factors: the temperature difference dT and the heat dissipating surface A. The formula P = α * A + (dT) described this relationship, where α stands for the heat transfer coefficient. For an air heater, dT would be the temperature difference between the air and the surface of the heater.
Higher temperatures (dT) allow for higher power outputs. For most applications, however, we recommend a temperature between 180 °C and 240 °C .
Increasing the heat dissipating surface area can also increase performance.